MEGA.PULS® FOCUS from REHM puts competitor´s products clearly in the shadows
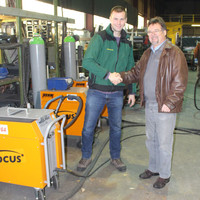
The Fortuna Fahrzeugbau (vehicle construction) company based in Ochtrup maintains two production sites where welding with REHM equipment is now standard practice. The management is very impressed with the advantages offered by the equipment and underlying technology. Plant II uses MEGA.PULS® FOCUS in the welding shop and Plant I employees rely on the step-switched REHM SYNERGIC.PRO.
Success story - MEGA.PULS® FOCUS at Fortuna Fahrzeugbau
Fortuna Fahrzeugbau is a traditional company founded in Ochtrup in 1946, that has concentrated on the production of tippers for agricultural use in Plant I. Plant II is a successful contract welding facility and is a major supplier for companies in the environmental technology business. With regard to welding solutions the company is supported by ENGA, based in Rheine.
ENGA and REHM representatives visited Plant II in Ochtrup in May to review the recently purchased MEGA.PULS® FOCUS equipment on location
The highest quality demands on welding work
Plant II of the contract welding facility in Ochtrup primarily used manual welding because the part spectrum is extremely comprehensive. It produces parts required for the manufacture of tippers that range up to several metres in length and that are welded using a welding tractor. Simple struts or anchors are also machined in the plant alongside the welding processes. All parts are sandblasted to ensure a perfect condition before further processing. As the components are subsequently painted, Fortuna Fahrzeugbau places great importance on the cleanliness of the parts and weld seams and the quality of the weld seam. The contract welding facility in Plant II also pulse welds S235 to S355 steel using SG3 1.2 mm welding wire.
The MEGA.PULS® FOCUS welding machine was chosen for the task.
Although previous welding machines met the quality criteria, management of the contract welding facility were very dissatisfied with several different issues. Of particular concern to the management was the health of their employees. The air quality in the building was very poor. „Previously there was a perceptible fog in the building that became intolerable on health grounds” said Christian Schwartbeck, the manager of the contract welding facility.
The solution came after detailed consultation with Dieter Enge of ENGA welding technology, who pointed out that the FOCUS.PULS process developed by REHM produced up to 70 percent less welding fumes when pulse welding than conventional arc welding. Using this innovative technology also reduces intensive post-processing activities, which up to the present time has been a significant financial disadvantage requiring two hours per day and additional employment, unnecessarily burdening the medium to long-term competitiveness.
After detailed analysis ENGA made a MEGA.PULS® FOCUS 400 available on loan and welder Guido Bitting, an employee in Plant II, extensively and thoroughly tested the welding machine and its functions. Conventional welding was performed with the MEGA.PULS® FOCUS 400 in the same way as pulse welding or double pulses.
MEGA.PULS® FOCUS passed all of the tests with flying colours
After a short changeover period the new welding machine was fully accepted and today still impresses by delivering the following results.
- Significantly reduced rework
- Welding fumes in the workplace are noticeably reduced
- The high precision arc and visible welding process is very impressive
- The deposition rate is significantly increased
Within a very short period both the management and the employees were convinced of the advantages offered by the innovative REHM welding technology.
The company also tested a competitor‘s product at the same time as the MEGA.PULS® FOCUS 400 test. The conclusion was a clear endorsement of the innovative REHM welding machine. In addition to the advantages already mentioned, the MEGA.PULS® FOCUS from REHM also offers considerably higher user-friendliness than the competitor‘s product. A further strength of the MEGA.PULS® FOCUS is the extensive availability of programs for welding processes and characteristic curves. These had to be purchased separately for the competitor’s product that was tested. Fortuna chose to procure six MEGA.PULS® FOCUS systems because of the overall positive experience, the high efficiency and the extremely low welding fume emissions.
The situation at Fortuna today
At the present time the contract welding facility is operating ten machines with the innovative technology for the pulse welding process optimised by REHM. Each of the new stations has more than lived up to the motto „pulse to success“. The conclusion of the Fortuna management is a resounding endorsement of MEGA.PULS® FOCUS.
The top priority in the decision to use new pulse welding machines was to significantly improve the condition of the air in the Plant II building. The success of this project is evident and the improvement in air quality much appreciated by the employees. As their second priority the Fortuna management targeted the high costs incurred for rework. These are also a thing of the past. „All we have to do now is rub them down with a cloth” explained Managing Director Christian Schwartbeck. The list of savings is even more extensive.
Apart from the quality improvement to the weld seam, the current welding speed achieved with the new equipment is at least 25 percent faster than with the old equipment.